以「精實生產」作為升級轉型之基礎
工業4.0以軟體為核心,不過,在加裝感測器、機器人、自動搬運車等設備以前,仍須回到製造端作檢視。「精實生產」是源於日本Toyota的一套管理方法,涵蓋生產、物流、成本等層面,可為產線建立起一套精簡、流暢的作業方式,大幅降低企業成本、提高生產效率,並提高產品品質。
約二十年前,台灣引興董事長王慶華便引進精實生產,甚至跨界成立精實管理顧問公司。當我們踏入位於台中西屯工業區的工廠,乾淨的工作環境與井然有序的生產線,已讓人留下別開生面的第一印象。
就以同樣生產工具機零組件的廠商作比較,一般工廠的生產週期約需2天,但台灣引興僅需4小時,2018年剛完成的新產線,生產週期更降至30分鐘以下。另外,一般工廠採大量生產,做好的商品先放在倉庫,等顧客下單後再出貨,台灣引興則從客戶下單後,從材料開始製作,速度還比同業更快,並且,「我們的工廠完全零庫存,做好的產品在出貨區等待集貨不超過2小時。」王慶華的一席話讓人瞠目結舌。
問題隨之而來,「這麼精準的生產流程,到底是靠什麼電腦軟體來管理?」王慶華的回答更令人咋舌:「這間工廠,不靠任何電腦來管理,但可以管理得比用電腦還來得精準!」
走入廠內,王慶華陸續為我們揭密。原來生產線運用精實生產中「可視化管理」的方法,放眼望去,整層樓有20個台車在各個加工機台間緩緩移動,加工好的材料就放在台車上,等待進行下一個步驟。「以前有200個台車,但因為數量多,大家沒有感覺,覺得慢慢做就好,但數量少,一下子就做完了,有多少量一目了然,大家就會緊張。」王慶華說:「而且,在這個工廠裡,『順序就是我們的聖旨』,一般的工廠發現做錯,為避免生產線斷掉,會跳過先做下一件,但我們一旦做錯,就不可以繼續做,等處理好再繼續做下一件。」他一語道破其中的奧秘:「我們藉此創造出無形的張力,讓每個人都主動戰戰兢兢,因此不需要別人管理。」這就是台灣引興引以為豪的「順序生產」。
也由於採少量多樣化生產,王慶華將全台近300家客戶,依位置劃分成9個區域,同一個區域的產品會集中生產,再運用類似公車路線的送貨路線圖,以同一輛車出貨,運費成本竟比以前更省。
精實生產強調「需求=供給」,王慶華說,庫存就像水庫的水位,水位逐步降低,細小的問題也隨之浮現,再加以管理,針對生產流程、訂單排程、派員、送貨等不同環節,把不具附加價值的浪費(如運輸、庫存等)逐一消除。
他另指出:「能花錢解決的事情不稀奇,要做花錢不能解決的事情。」就以新產線為例,透過精實改善,將原本需要花費3,000萬的機台設備,以600萬就達到相同效果,成本驟降,製程的工程長度也從90公尺縮減到22公尺,生產週期則從2小時濃縮到30分鐘以下。過去,因工程長度與生產週期較長,曾有顧問建議,可投資購買自動搬運車與Barcode追蹤系統,隨著產線改善,問題也迎刃而解。
產線導覽結束後,王慶華領我們到全廠唯一的倉庫。不過約十坪大的房間,集合了上百種零件,每天有工作人員依訂單配給固定的數量,在這裡,連一顆螺絲都不容浪費!
王慶華語重心長地說,在往工業4.0的路上,台灣產業最缺乏的,往往不是智慧製造,而是按部就班的態度,因為就算交由機器,步驟仍是由人來管理。因此,還是得回歸根本,為產線建制起標準化作業流程,並運用精實管理,將其做到極致,再針對需要升級的地方作升級,這樣的升級才有意義。
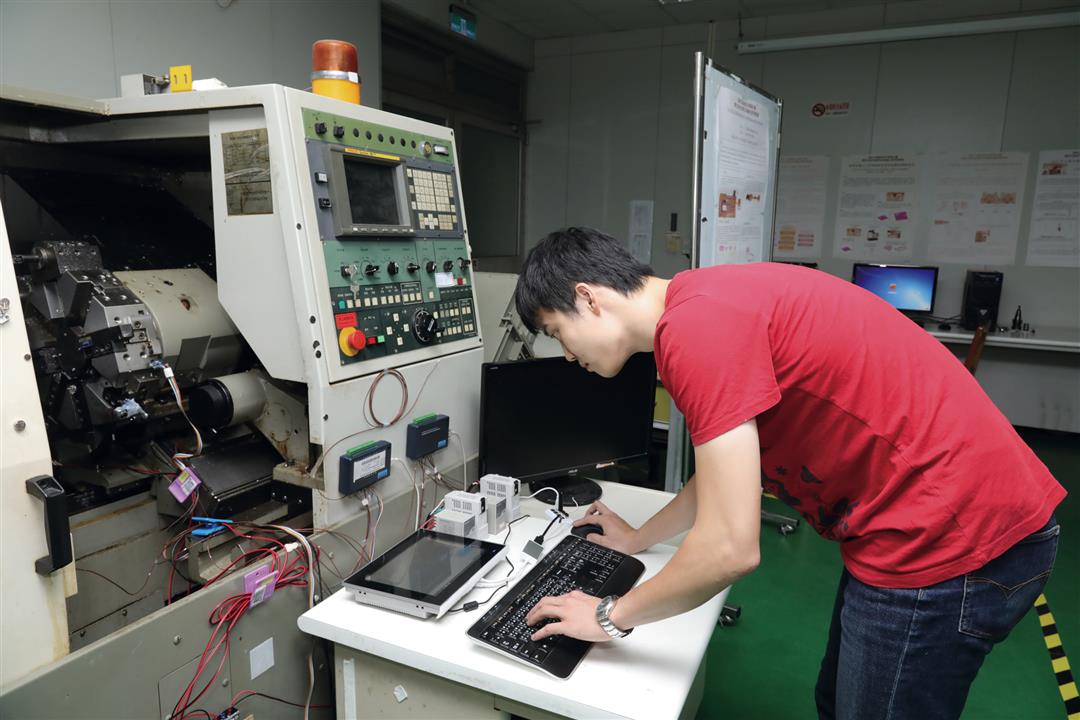
除了讓學生到業界實習,藉由與企業合作,企業提供設備給學校,打造出學用合一的學習環境。